All That Glitters
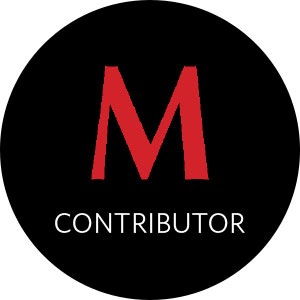
W hat I Do
I design jewelry — clients tell me what they have in mind and I help them define it. I put it down on paper — well screen — and then create the piece.
How That Works
I usually get an idea of what design the person wants from pictures of existing jewelry. They’ll show me what they like and what they want to modify pointing out how or where the stones are set — “Add a row of diamonds around the center diamond” or “Put my name and my kallah’s below the center diamonds of the engagement ring.” Other times like when I’m working for a company a sketch artist will give me a sketch four views of a design and I convert that to a file that can be made into a 3-D piece of jewelry. Because the design process is virtual I have the ability to work with customers wherever they are all over Israel and the US and beyond.
The Process
Once I have a design of what the client wants the piece to look like I build the design in CAD — that’s computer-aided design the same technology used in engineering of pretty much everything from architecture to shoes to cars boats and rocket ships. I send a highly realistic image to the customer and he’ll tell me if he wants to modify something or he’ll give me the green light. Then I send the file to a 3-D printer CAM — that’s computer-aided manufacturing — which prints the piece in high-resolution wax. Say it’s an engagement ring so the casting house next door casts the wax to gold — they put it in a cup with plaster all around it with a tube leading from the wax to outside the cup. The plaster hardens and the wax is melted out so you’re left with a shape in the plaster where the ring was. The gold is poured through the channel into the empty space and once that sets I take the gold piece out my jeweler polishes it and a stone-setter sets the diamonds.
Most Common Question
How fast can the piece be made? And how much will it cost?
The Best Part Of The Job
I feel like I’m playing a computer game that results in real and beautiful creations. The toughest part? Not going crazy when a design won’t come together and I have to struggle with it. It can also be tough trying to comprehend what someone’s vision is but that’s why we work together to get there. Of course it’s all worth it once you figure it out and you have a happy customer — often a chassan and kallah which makes it all the better.
Equipment I Always Have On Hand
My laptop because my designs start on a computer plus a loupe — a jewelry-specific magnifying glass made up of three lenses and a millimeter gauge.
The Season I Never Sleep
Before Chanukah winter holiday season and Yamim Tovim when people order presents. And in the wholesale world before jewelry shows when companies want to create new lines to display. At Yvel the company I used to work for this meant long nights at work to create full lines of jewelry around ten different pieces with a similar theme.
My Most Challenging Project
About a year ago I scanned a pearl into the computer in microscopic detail. I built a beautiful twisting necklace around it and created the necklace to hold more than 200 diamonds black and white. It was part of an existing line the company had and with a computer I was able to build it in a way that the stone-setters had less work.
Oops Moment
One of the most important things I’ve learned along the way is to always verify the jewelry materials — the metal the stone — in front of the customer. People often bring old jewelry for redesign and they’re usually right about what they have but I remember I once had to tell a guy who was getting remarried that the ring he’d inherited from his mother wasn’t a real diamond.
One Thing Every Man Should Know When Getting His Wife Jewelry
She has to wear it for the rest of her life not you. Ask her what she likes.
And One Thing Every Woman Should Know
Diamonds naturally attract oil and they’ll lose their shininess unless you do upkeep with them. Here’s how: use a toothbrush and dishwashing soap — that’s important since it generally doesn’t have oil — to scrub around the diamond and especially underneath where dirt gets trapped. This will make your diamond sparkle and keep it looking new. I try every Pesach to scrub all the diamonds in the family — mine and my wife’s — and it’s like giving all of the women new diamonds.
Being A Male In A Field That’s Geared Toward Women
I get them here and there — “You do what?” — but the truth is that in the jewelry districts like Fifth Avenue in New York and the Borsa in Israel which are major diamond-manufacturing and selling areas the vast majority are men. Women are more involved in the fashion aspects — sketch artists management sales graders — but they’re rarely diamond wholesalers or in manufacturing. There are also more women involved in artsy jewelry like Michal Negrin.
What I Was Up To In 2000
I was 11 and I built a somewhat complex clubhouse. As a kid I loved to build I’d read books about architecture. That skill set is in my blood — my grandfather was an engineer he actually worked on the UN building in New York.
2009 I worked in Zalman’s Treasures in Detroit which is where I’m from selling everything from kids’ watches to high-end luxury pieces. It was a good start I learned a lot but I kind of stalled wasn’t making progress. Then I totaled my car in a three-car crash. Everyone was okay baruch Hashem but it was a wakeup call so I put everything on hold and went to learn in Jerusalem for a couple of months. At the Kosel I got set up for a meal by Jeff Seidel at Martin Rapaport — he’s the first and last stop for establishing diamond wholesale prices throughout the world. I’d been unsure whether I should continue in jewelry or not so my random meeting of such a big person in the field felt like a nudge to continue.
2010 I went to the Gemological Institute of America in New York to learn diamond-grading. It’s an intense course — two months full days an hour or two of homework a night. GIA is well known for its diamond laboratory; they actually certified the Hope Diamond and I met one of the teachers who was part of the team.
2011 I moved to San Diego to take the colored stones GIA course in California — it was a grueling four months and quite a challenge considering I’m color-blind. Gemstones are identified more with tools than by color; many come in almost all colors so they need to be identified by other means. As for diamonds which are graded on a white-to-yellow scale color-blind people are actually better at it because we have a hard time differentiating color so our eyes compensate by differentiating between light and dark which is important when grading diamonds.
2012 I moved to the Valley in L.A. and went banging on doors literally trying to find a job. It took a month to find work with a diamond-grading laboratory; we were ten or so graders sitting together in a dark room with microscopes. I didn’t enjoy the work environment so I found a job nearby at Parade Designs. The Disney Symphony Hall was walking distance from my work and I’d go visit occasionally just to get inspiration from the artistry the elegant flowing curvature of the walls.
2013 I got married. My wife and I moved to Israel and I worked at Yvel. One of the pieces I designed there was worn by a celebrity for a high-society event.
2016 I opened my own business in Ramat Gan. Until then I’d been working more with the manufacturing aspects I didn’t interact with the customers that much. Now I deal one-on-one with the customers and I love it. When I was dating someone gave me Rav Shalom Arush’s The Garden of Peace. It had a big impact on me. I still continue to read it. I recently ordered a stack of them and I try to give them to chassanim with the engagement ring. One thing that was unsatisfying about working for a large company was that the customer was faceless. Now I get to sit down with real people who are often at an exciting time in their lives — and it’s not just about the jewelry it’s about the relationship and their future. (Originally featured in Mishpacha Issue 658)
Oops! We could not locate your form.