Offshore
| November 9, 2021Shipments from across the world are not moving as smoothly as they should, and that has led to some problems
The store is full, the shelves are lined from top to bottom with toys and games in colorful boxes just waiting to be purchased and played with. And as most people have noticed, stamped at the bottom of the toys are the words: “Made in China.” We imagine large factories in China churning out dolls and menchies, board games and matchbox cars. Toys that somehow, magically, make their way over to the United States and fill our stores so we can buy birthday gifts, Chanukah gifts, or something special just because.
Yes, it’s magical. We can buy the things we need, when we need them. Somehow, most of the time, everything we want is in stock in the stores. If not, there’s usually another shipment coming, and having that coveted toy in our hands is only two weeks away.
It seems like a great system, doesn’t it? We order what we need, and a short time later it arrives at our doorstep — even though it took a trip halfway around the world to make it here.
But, these days, we’ve hit a little snag. Shipments from across the world are not moving as smoothly as they should, and that has led to some problems.
The Problem
To understand why goods from China and other Asian countries are currently in short supply, we need to go way, way back to the beginning. How are those products made? Shipped? Delivered? And where along those lines are they being held up?
The Process
Production in China is a complicated process. For example, let’s take a woman named Mrs. Horowitz, the creator of . She had the original idea of Jewish MentcheesTM. To turn this idea into a reality, Mrs. Horowitz contacted Mr. Hoffman of Giga Imports.
Mr. Hoffman heard Mrs. Horowitz’s idea and put in the work that turned it into a reality. His company, Giga Imports, is an extensive network of factories in China that they work with who can turn a computerized image into a 3D plastic menschie that reaches the hands of frum kids all over the world.
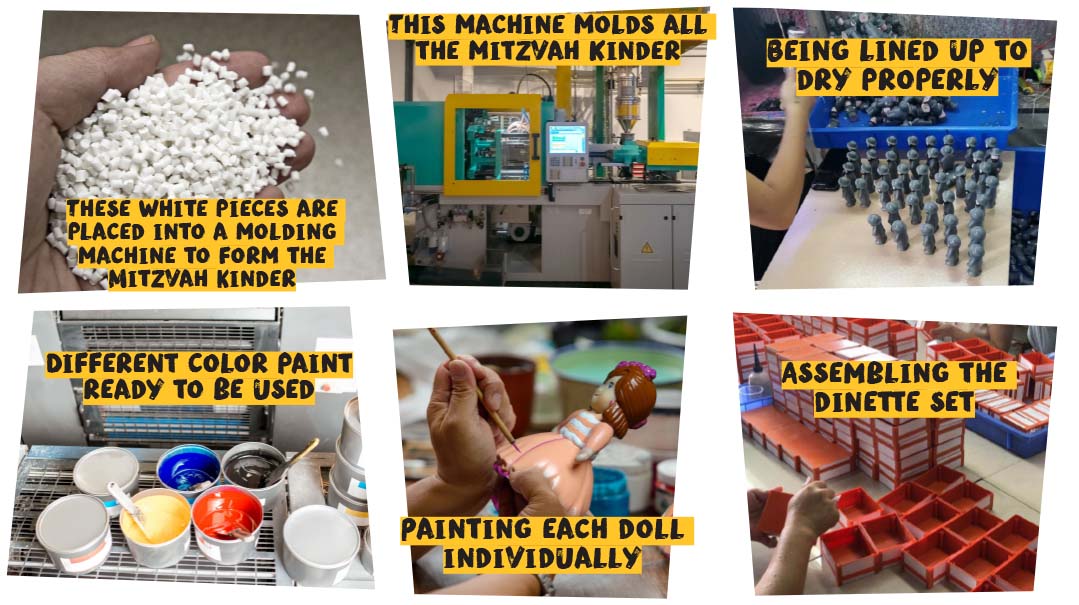
Factory production
A glimpse at the Mitzvah Kinder factory in China
The menschies and their packaging are produced in different factories across China. The menschies are made in one factory, the cardboard box in another, and the plastic packaging in a third. Giga Imports ensures that every component needed for the process is of high quality, and that the factories are reliable, honest and productive. They then take all the pieces into their own warehouse where they package it into the product you see in the store, and pack them all up to be shipped across the ocean.
Shipping: Products are shipped from China on huge ships called cargo ships, stacked inside gigantic containers. Giga Imports picks the size container it needs to ship all the Mitzvah Kinder it has produced in China. They may send it directly to New York, which is the slower route, or through the port of L.A., which can speed up the process by up to two weeks, but makes the shipping costlier.
Unloading: Finally, the Mitzvah Kinder make it to the US, where they dock at the port. Huge cranes unload the containers off the ships and waiting trucks take the boxes of Mitzvah Kinder from the port to Giga Imports’ warehouses.
And to the stores: And from there, well… it’s just a short trip to your local toy store.
All this was the nice, steady process of shipping goods during a time I like to call B.C. — Before Covid.
Now… let’s just say that getting what we need from China has become quite complicated. Every. Step. Of. The. Way. Here’s how it looks today:
Orders: During Covid, people were stuck at home with nothing to do and nowhere to go. Many of them got large amounts of money from the government, just waiting to be spent. So, they started to order. And order. And order. A whole bunch of stuff, much of it made overseas. And if you were the type who didn’t buy things for a whole year while you hunkered down at home, as soon as the lockdown lifted, you needed to buy a lot to make up for all the new stuff you now needed. So people were ordering more, which meant factories needed to start producing more.
Shipping: When ports in China got closed because of Covid, there was no advance warning. No one said, “Hey, guys, you’ve got two weeks to ship out all the containers waiting to go out and then you’ll be closed down.” Nope. They just… closed. The containers, the ships, everything got shut down right where it was. Then they opened again. And dozens of ships, fully loaded with merchandise, were sent out one after the other. Sounds great, right? Except that no one thought about what would happen on the other side.
Factory Production: Every single item that goes into the manufacturing of the menschies is actually produced in different factories across China. So the 3D molds that will form the menschies are prepared in one facility, and the menschies will be manufactured and molded in another. The paint and special coatings need to be produced in yet another factory. Finally, the inner colored packaging, cardboard boxes, and the plastic packaging are each produced in their own factories as well. Giga Imports ensures that every piece in the process is of high quality, the factory reliable, honest, and productive. They then take all the pieces into their own warehouse where they package it into the product you see in the store. When all this is done, the warehouse can pack them all up to be shipped across the ocean.
Unloading: During normal times, a ship from China would sail over to L.A., dock, and unload. It was unusual for there to be even one ship waiting for a turn to dock. Now there are over 50 cargo ships waiting their turn. And each ship holds between ten and twenty thousand shipping containers — each of which can hold thousands of boxes! There isn’t enough machinery and equipment to unload so many ships at once. And you can’t just send them to another port because by now all the ports are backed up. Besides the cost of fuel and manpower to run the ships while they wait, waiting ships cause even more problems back in China. Containers that are waiting to be unloaded cannot be shipped back to China and refilled with new merchandise. They are still busy shipping the merchandise that had been sent out before. This means that there is a shortage of shipping containers in China. When Giga Imports wants to ship out that new shipment of merchandise, it’s going to be much harder to get a shipping container to ship it in. And as we all know, if there are lots of people who want shipping containers and not many containers to be had, the price of shipping is going to go up. By a lot. A container that cost $4,000-$5,000 to ship in the past, costs $18,000 today. That’s around four times the price, just to ship the product!
To the stores: To get the product from the port to the stores, the first step is unloading the container onto a truck. A truck driver will be told to come when the goods are unloaded from the ship. But because there are delays in unloading, trucks and their drivers can wait for hours until their merchandise is ready to be picked up.
Once all the goods are loaded onto the trucks, there are a few different routes they can take. Either they can go to a warehouse near the port, which is a short, fast solution if you have a warehouse and your warehouse has space, or it can be shipped across the country by rail. Truck drivers drive to the train station and load up the trains.
But right now, there are delays by rail as well. We don’t have more trains, or faster trains just because we have more goods to ship. Just like those Mitzvah Kinder waited on the ship for their turn, they’re going to have to wait in a warehouse until there’s room on a train for them to go through.
While small companies are jimmying for room on cargo ships, and may have a hard time shipping their goods, large companies like Walmart and Costco have found another solution. They are chartering their own ships. These companies fill the ships with all the products they need for their store, so that they can ship everything they want, when they want to. But chartering a ship is very expensive. Think $80,000 per day. And the company needs to rent the ship for a minimum of a year. That’s $29,200,000 a year just to ship their goods across the ocean!
And on to you: Once you get to the store, waiting to buy a new game or toy, those products are going to cost more. They need to. Wholesalers need to charge more in order to cover the increased costs of shipping. Store owners need to buy the goods at a higher price, which means they need to sell it to you at a higher price. They are also less likely to stock up on each product, since they are worried that fewer people will buy it at the higher price. The store has less than it used to, and once the store runs, out you have a shortage. The next person who comes in to buy Mitzvah Kinder cannot get any.
So, we have a crisis. Not as many of the products you want are being produced, the ones that are produced are stuck on a ship, and when they’ve finally gotten off the ship, they’re stuck at the train station waiting to come to a store near you. Even once the store gets them, they will stock less and run out faster.
Solutions
The Idea: Keep work at the docks running 24/7
Why it helps: If the docks are in operation more hours each day, more merchandise can be unloaded each day as well. Trucks can then load up at night and drive on the now emptier highways, instead of driving during the day and getting stuck in traffic. This way, trucks can deliver their goods faster and turn around to pick up more. Shipping containers also empty out faster and can be shipped back to China for another load.
The Drawback: Even if trucks can move goods faster, they get stuck at the railroad, which cannot run more trains than it has, or use more cranes than it has to unload the trucks.
The Idea: The Infrastructure Bill
Why it helps: President Joe Biden is trying to pass a bill that will put lots of money into infrastructure. This means money to fix and build things like highways, railroads and ports. If we fix highways, trucks can move faster. Fixing and expanding railroad lines means more goods can be shipped out by train as well.
The Drawback: While this is a great long-term solution, it will be a long time before those construction projects are completed. It will also cost a lot of money.
(Originally featured in Mishpacha Jr., Issue 885)
Oops! We could not locate your form.