Going, Going, Gone?
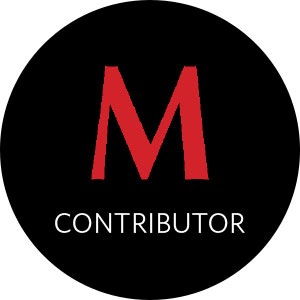
Let’s explore some of the industries that used to be super important for people’s everyday lives but are now struggling to stay alive. The big question is if these industries will survive in the long run.
Imagine hopping into a time machine and going back to the 1700s. What kind of job do you think you’d choose? Wagon driver? Chimney sweeper? Blacksmith? Well, guess what? Most of these old-fashioned jobs don’t exist anymore because they aren’t needed today. Some of them have disappeared completely, while others barely exist.
Let’s explore some of the industries that used to be super important for people’s everyday lives but are now struggling to stay alive. The big question is if these industries will survive in the long run.
The Thatcher
Look at all the houses around you, whether on your street or anywhere in the world. They all have one thing in common — a roof! Nowadays, roofs are usually made from concrete, slate, or metal. But before the 20th century, and especially during medieval times, most roofs were thatched. Thatched roofs are made from dried straw, reeds, or rush. You know those adorable little cottages that look like they’re from a fairy tale? They often have thatched roofs.
Thatched roofs weren’t just found in England; they were popular all over the world, even in Canada and the United States. In fact, in its heyday, thatch was the most popular choice for roofs worldwide. Wondering why? Thatched roofs are made from materials found locally and they’re relatively cheap. Wherever there’s a farm, there’s always plenty of extra wheat or straw to use. And what a smart way to put those leftovers to use!
Back in the day, thatchers (skilled people who made thatched roofs) were everywhere. Even the smallest village had a thatcher or two. As you can imagine, putting a roof together from straw or reeds is no simple matter. It took about seven years for new thatchers to learn their skill and become “master thatchers.” The more experience they had, the better they became at it.
During the Middle Ages, which lasted from the 5th to the 15th centuries, practically everyone had a thatched roof. But around the 1700s, stronger materials like slate became available. Slate roofs became a symbol of wealth, and rich people started replacing their thatched roofs with slate. Having a thatched roof became a dead giveaway that you were poor.
Many European thatchers lost their lives in World War I and the demand for thatched roofs dropped as well. By the 1950s, thatching was a dying trade. But guess what? Thatched roofs have become trendy again! Thatching is making a comeback, as more young people are learning to become thatchers. So don’t worry, thatching won’t completely disappear anytime soon.
In England today, there are about 60,000 thatched roofs. What’s fascinating is that more than 250 of these roofs have a base layer of thatch that’s a whopping 500 years old! A thatched roof is made up of many layers and can last for decades. So when it’s time to rethatch the roof, there’s no need to start from scratch. Only the top layer needs to be replaced.
One of the cool things about being a thatcher is the chance to uncover hundreds of years of history.
They get to see how ancient thatchers worked and discover the different styles of thatching used in the past. So if you’re ever feeling adventurous and manage to sneak into the attic of a thatched cottage, get ready for a special surprise! You’ll be standing right beneath a piece of ancient history. Look up, and there it is — the very first layer of thatch!
Thatching trivia:
- New thatch starts off yellow and takes about six months to turn brown as it weathers.
- Rethatching a roof can take six to eight weeks, while replacing a regular roof can be done in just a few days.
- Many thatchers have their own fields where they grow reeds or wheat specifically for thatching.
- The country with the most thatched roofs is probably Indonesia.
The Glassblower
When was the last time you thought about how your glasses were made? How about the windows and mirrors around your house, in your car, at your school…? They’re all made from this amazing material called glass, which is pretty incredible. It’s used in so many ways that it’s hard to imagine life without it.
Glass was invented more than 2,000 years ago in a region that was known as the Levant (which included parts of Israel, Lebanon, Iran, and Syria). The Romans saw how cool it was, and they were the first to set up glassblowing workshops to create both practical items and decorative knickknacks. Glass is made by heating a mixture of sand, soda ash, and limestone together at a crazy hot temperate until it turns into a liquid. It can then be blown like a balloon and shaped into anything you can imagine. After it cools and hardens, it becomes solid, and voilà — glass!
By the time the 13th century rolled around, the city of Venice in Italy became the center of glassblowing. There were so many glassblowers that officials got worried that the whole city might go up in flames. The glassblowers were banished to the nearby island of Murano. To this day, Murano is known for its beautiful and fabulously expensive chandeliers, mirrors, and glass sculptures, which are sought after by millionaires all over the world.
In the late 19th century, new machines were invented that were capable of mass-producing glass. Glassblowing became less necessary, but there are still many glassblowers around, most of who consider themselves to be artists.
The Lowdown on Glassblowing
I was delighted to discover that there is a glassblowing workshop right here in Yerushalayim, where I live. Sadly, I haven’t yet had a chance to attend a workshop. But the glassblower, Yael Vloch, was super nice and agreed to tell us some more about glassblowing.
Hi Yael. I haven’t visited your workshop in person, but the photos of your studio look awesome. What made you study glassblowing?
When I was 19 years old, I decided that I wanted to study art. I wasn’t really familiar with the field or the art schools, but I knew that the Bezalel Academy of Art and Design in Jerusalem was a good place to start. I enrolled there without really thinking about what I actually wanted to do, and studied glassblowing for four years. After I finished, I traveled to the United States and Italy for a few summers to study with glassblowing masters so that I would be able to specialize in the field.
Can you describe the glassblowing process in full? What raw materials do you use? What tools?
When I work, I use ready-made glass rods and glass tubes, along with a system that reaches a temperature of 1,600oC. As you can see from the photos, each workstation in the studio is equipped with gas torches, which is what we use to heat the rods. Once the glass has melted, we use a blowpipe to blow air into the glass to inflate it. Then we use other tools, like large tweezers, to shape the glass how we want it.
What kind of glass objects do you personally make in your studio?
In the studio, I enjoy sculpting and blowing vessels like vases, goblets, and ornaments. What I love most is the challenge of creating new shapes and trying new techniques that I have never attempted before.
Do you make custom orders?
Yes, but I only agree if the customer lets me use my creativity and gives me the freedom to make it my own. Once, I had a customer who wanted a bird sculpture. They told me the colors they wanted, but the way I made it was my own artistic interpretation. It turned out to be a beautiful custom creation!
What do you love about glassblowing as an art?
Because glassblowing involves fire, heat, and a lot of concentration, I can’t talk on the phone or do anything else while I’m working. I find it gives me peace of mind. It’s almost like meditation.
How is hand-blown glass different to mass-produced glass?
Hand-blown glasswork is very different from factory work. In factories, machines hold the glass, and everything is precise and repetitive. It’s all about making lots of the same thing. But when you work by hand, it’s a whole new level of creativity. It’s not about being super precise and there’s the freedom to do whatever you want. Every hand-blown glass object is unique, which is what makes it incredibly special.
What kind of glass objects can people make in your workshops?
In the studio, I invite people with no experience to try and experience the technique. Kids are welcome from as young as nine years old. I demonstrate how to make simple shapes, and then the participants can try it themselves. You can make small animals, cactus flowers, jewelry, or holiday-related objects — like honey teaspoons and pomegranates for Rosh Hashanah, or dreidels for Chanukah.
How do you make sure everyone stays safe while working with a hot flame and hot tools?
Glasswork can definitely be dangerous and can cause small burns. Therefore, before starting the work, I give everyone clear safety instructions. Each participant gets protective gear like safety glasses and aprons. Obviously, I do my best to make sure everyone comes out of the workshop unharmed.
You’ve worked with Dale Chihuly, whose glass sculptures are famous all over the world. What’s it like to work with master artists?
I have had the opportunity to study in Seattle at a Dale Chihuly school and with other highly skilled instructors. It’s always inspiring to see other artists working, and I find it really enriches my own technique. Most importantly, meeting a small community that is passionate and excited about glassblowing always feels like getting together with family.
Glassblowing trivia:
- The glassblowing process hasn’t changed much since the 1600s.
- Molten glass is reached at 2,100°F (1,148°C).
- Glassblowers might look like they’re puffing away, but they only need to blow a small amount of air.
- The glassmakers of Murano managed to keep the tricks of their trade a secret for 400 years.
- Scientific glassblowers are glassblowers who create custom glass equipment for research teams and scientists.
Yael, thank you so much for sharing your love of glassblowing with us. A glassblowing workshop is right up there on my bucket list. I hope to see you soon.
The Lamplighter
I bet that if you live in the city, you don’t think twice about going outside after dark. Why would you? Everything is so bright and well-lit. But it wasn’t always like this. Back in ancient and medieval times, going out at night meant pitch-black streets and lots of stumbling around. It was pretty scary, to be honest! Back then, cities like London and Paris decided that enough was enough and streets had to be lit up at night during the winter months. They made a rule that everyone had to hang lanterns outside their homes. These lanterns used candles or stinky fish oil (yuck!) and had to burn from 6:00 p.m. to 11:00 p.m. No exceptions!
Then, in the 1700s, several scientists around the world began discovering different types of flammable liquids. This discovery led to a fantastic invention: gas streetlamps! In 1807, there was a huge celebration in London to light up gas lamps for the first time. It was a lightbulb moment for street safety and after-dark convenience. From then on, gas streetlamps spread to major cities all over the world, from London to Paris to New York and Baltimore.
The new streetlamp phenomenon was phenomenal for more than just lighting up the night. It created a whole new industry! Literally overnight, cities needed people to light the lamps at dusk and extinguish them at dawn. And so, the lamplighter was born! Some people called them “leeries,” from the Scottish word for light or lamp.
If you were out and about at the right time of day (or is it night?), you could spot a leerie from a mile away. Leeries were known for whistling a merry tune to let people know that they were in the vicinity. They were also armed with a ladder, wick trimmer, and whale. No, not that whale. Whale, as in the flammable liquid that was used in gas lamps. Each evening, the leeries made their rounds, painstakingly lighting one streetlamp after the other. In the early hours of the morning, they were back up the ladders, this time extinguishing the flame.
Lamplighting may have been a blue-collar job, but nevertheless, leeries were quite respected. The neighborhood leerie needed to earn the residents’ trust — after all, he was prowling at all hours of the night. Once a leerie proved that he was trustworthy, he often found himself doing double duty as a nightwatchman. Leeries took such pride in their occupation that they usually passed it down to their sons. Lamplighter families formed their own traditions, and even made shidduchim with each other.
But what happened when electricity came into the picture? Well, things changed for the leeries. The demand for their job went down, as automated streetlamps that run on electricity became popular. These new lamps were easier and cheaper to use compared to the gas lamps, no matter how pretty the gas lamps looked. Nowadays, we don’t see many gas streetlamps around. The ones that have survived have been designated as protected landmarks. That’s great news for the few lamplighters that remain. Their jobs are probably safe for now.
Lamplighting trivia:
- Berlin has 30,000 working gas streetlamps! That’s more than half of all the gas streetlamps in the world!
- In London, there are still 1,500 gas lamps shining brightly. They’re located in the eight Royal Parks and on several other historic streets and landmarks, like Buckingham Palace and Trafalgar Square.
- Streetlamps used to be shorter, but when tall vehicles like trucks were invented, they had to raise the streetlamps higher than the traffic.
- If you’re in the US, you can find working gas lamps in cities like Boston, Cincinnati, and even the famous French Quarter in New Orleans. There’s even one in New York City!
It’s pretty amazing how new inventions can impact the old way of doing things. But you know what’s even more amazing? These three industries have been around for hundreds of years, and they still work in pretty much the same way. I can’t help but wonder if they’ll still be around in another 100 years. Only time will tell!
(Originally featured in Mishpacha Jr., Issue 972)
Oops! We could not locate your form.