Diamond Art
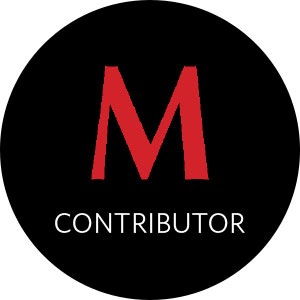
Zivia Beer is a popular jewelry designer from Bnei Brak, who helps her clients create the custom jewelry of their dreams
Photos: Zivia Beer
You all know what graphic design is. I bet you even know what interior design is as well. But did you know that jewelry design is a thing, too? All those glittering gold and diamond pieces in the jewelry store didn’t design themselves, you know.
The process of making jewelry is fascinating, and I know just the person to show us how it’s done.
Zivia Beer is a popular jewelry designer from Bnei Brak, who helps her clients create the custom jewelry of their dreams. Today, we’ll be following the process of creating a piece of jewelry, from sketch to reality.
Decisions, Decisions
You know that feeling when you walk into an ice cream store and you’re faced with so many yummy flavors? It’s a good thing the store lets you sample the flavors to help make your decision easier! Walking into a jewelry store is pretty much the same thing. How do you choose from so many beautiful things? If buying jewelry in a store is complicated, then how on earth are you supposed to choose a design when the options are literally endless?
When a new client tells Zivia she wants to make a custom piece of jewelry, the first thing they do is have a little chat. They’ll discuss what category the new piece will be (necklace, earrings, ring, or bracelet.) Will it be for Shabbos or weekday? The client will need to have some idea of how much money she wants to spend. Then they’ll talk about the style. Here is where most people will get stuck, because there are so many options! Luckily, Zivia has a neat trick up her sleeve.
After four years in the business, Zivia has designed dozens of pieces. The actual pieces are made of gold and diamonds (and sometimes other gems as well), but she also has silver models of many of her designs. The silver models help new clients visualize sizes and shapes. This is especially important for earrings. Sometimes clients will come with some of their own ideas. Otherwise, Zivia will show them some inspo pics to help them get ideas.
From Sketch to 3D Model
Once she knows the client’s budget and understands more or less what she’s looking for, Zivia takes out her pencils and starts sketching. She usually sketches a few different styles. Then, it’s decision-making time for the client all over again. After the final sketch has been approved, Zivia sends her sketch to the modeler.
The modeler uses a computer program that is unique to jewelry design. He creates a 3D computer model that is to scale, down to the exact millimeter. This 3D model is very important. Not only does it let the client have a good look at her future jewelry from all angles, but it will later be used for the actual creation of the piece.
When the jewelry being made is a ring or earring, the modeler adds a hand or an ear to the 3D model, which helps the client visualize how her jewelry will look when she puts it on.
Printing, Sprueing and Casting
Now we’re off to the casting house, which is a very happening place!
The first stop in the casting house is the printer — a cool machine that prints out the 3D computer model. But there’s no paper feeding into this printer. The model is printed using wax, so we end up with a 3D wax model.
The next step is preparing the wax model for casting. Casting is when molten metal is poured into a mold. But we’re not quite ready for that yet.
First, the wax model is put into a stainless-steel flask. Usually, the flask can hold a few models at a time. The models are each attached to a wax rod, basically a wax tree. The process of making this tree is called “sprueing.” It’s very important, because the sprues will act like channels, carrying the molten gold to all the places it needs to go. The tree is attached to the base of the flask.
Plaster is poured into the flask over the wax model. In casting, the plaster gets a new name! It’s called the “investment” — don’t ask me why. Then the whole thing is put into a kiln so the investment can set. What do you think all that heat from the kiln does to the wax? It melts it, of course! This process is called “lost wax casting,” because the wax model disappears in the kiln. (It can also be called investment casting.)
After the investment has set, the flask is removed from the kiln. It looks like the flask contains a solid block of plaster, but hidden inside is an empty space that is the shape of the wax tree.
Now for the casting. The gold has to be melted into a liquid so that it can be poured into a flask. Now, if you’re imagining lots of gold bars piled up in a corner, I like the way you think. But, don’t let your imagination run away with you. The gold that’s used in jewelry making actually comes in the form of tiny balls. Like pretty much everything else in this business, these balls have a fancy name. They’re called “casting grains.” Check out the sidebar for the lowdown on gold karats.
The molten gold is poured into the cavity in the flask, and the flask is then dropped into a bucket of cold water. This sets the gold, and at the same time, it causes the investment to break apart. A few swirls in the water, and suddenly the jewelry starts to appear.
But wait! What is that thing coming out of the water? It doesn’t look like a fancy piece of jewelry to me! Don’t forget that the wax models in the flask were all connected to a wax tree, so now we have a gold tree.
The Goldsmith
This gold tree looks way too bizarre, so I’m relieved that we’re headed to the goldsmith next. The goldsmith’s job is to separate the tree into its different gold pieces and then make each piece beautiful.
If you don’t like the dentist, you might want to skip this part. The goldsmith has dozens of different tools. Many of them are hand tools, but there are too many drills lying around for comfort. I’m getting the shivers just looking at them.
The goldsmith uses a brown putty called “chaser’s pitch” to hold the jewelry in place while he works. The first thing he does is remove the sprues. Each piece of the tree is carefully drilled off, and then the sprue on each piece is cut away too. Wow! The pieces of jewelry are really starting to take shape.
The goldsmith uses a bunch of tools to sand, file, and polish the piece until it’s absolutely perfect. Then, he drops the piece into a special liquid that contains micro metals. A machine spins the liquid so the micro metals can clean all the tiny crevices in the piece that the goldsmith’s tools can’t reach.
Diamond Dealing
Now that the gold base of the jewelry is complete, we’re off to buy some diamonds. Israel’s diamond district is the “Bursa” in Ramat Gan. The Bursa is a huge complex made up of several buildings on a few streets. This is where you come for anything related to jewelry.
There are lots of stores that sell everything from gold chains that Zivia buys for her clients’ necklaces to ready-made jewelry. The casting house is also located in the Bursa. Of course, the diamond exchange building is located here as well. “I usually come to the Bursa a few times a week,” Zivia says, “and I can spend hours going from place to place.”
Zivia tells me that there are two times during the jewelry-making process that she needs to consider which diamonds to use. The first is when she draws the initial design. She has to take into account the client’s budget so that she knows how many diamonds to incorporate into the design and what size and shape they should be. Before finalizing the design, she checks with her diamond dealer so that she can tell the client what the final price of the jewelry will be. Sometimes, it can take a while to play around with the design so that it fits both the diamonds and the budget.
Once the gold base has been made, Zivia will contact her diamond dealer with a list of the exact sizes and shapes of the diamonds she needs for the piece. Her dealer works hard to find the best quality diamonds at the best price. Did you know that diamonds are often sold in lots? That means that you buy quite a number of diamonds for one set price. The dealer has to check every single diamond in the lot to make sure that he’s getting a good deal. If a client’s piece needs 20 diamonds, for example, the dealer may end up buying 30 diamonds just so that he gets the best price.
Jewelry from a jewelry store has gone through several middlemen, and each one takes a cut, which drives up the price. Zivia cuts out these middlemen, so you end up getting more glitz for your gelt.
For larger diamonds, like the ones in engagement rings, the clients usually want a GIA report. This is a certificate from the Gemological Institute of America that has all the diamond’s info and tells you that the stone is the real thing. GIA reports aren’t limited to diamonds in America. They are used for diamonds all over the world, and each GIA certified diamond has its own serial number.
Setting Stones
Now that we have the diamonds, we’re headed to the setter. The setter peers through a massive electronic magnifier which helps him work with very small stones. He uses all sorts of tools to open the prongs, set the diamonds one by one, and close the prongs around them. This is painstaking work! When he’s done, he sands the piece down and cleans it with steam.
Now our piece of jewelry actually looks like a piece of jewelry. But it still doesn’t look quite right, though I’m not sure what’s wrong with it.
We return to the goldsmith for the finishing stage. He sands and polishes the piece once more, and then drops it into a liquid called rhodium. When the piece is taken out of the rhodium, it gleams like moonlight! Now I realize that before, the gold looked dull. The rhodium is what makes it all shiny and bright. But the gold can only be in the rhodium for a maximum of two minutes; any longer than that and it will turn black.
After being cleaned once more, the piece of jewelry is handled carefully with pincers and wrapped in paper. No fingerprints allowed! Then it’s time for Zivia to take it home, where she packages it in her beautiful jewelry pouches and gift boxes. And because she’s so nice, every client gets a box of Belgian chocolates too.
Gold Karas
You probably know that 24k (karat) gold is pure gold. But did you know that 24k gold is rarely used in jewelry-making? That’s because 24k gold is too soft and can easily bend out of shape. Most gold jewelry is made from a gold alloy that is either 14k or 18k gold. An alloy is a mix of two metals; a gold alloy is gold that has been mixed with another metal. Gold that is 14k is 58.3 percent gold and 18k is 75 percent gold. So what makes up the rest?
That depends on the color of the gold. Yellow gold is mixed with either copper or zinc. White gold is mixed with palladium or nickel. And rose gold is mixed with copper and silver.
Here’s a fun fact for you: The word karat indicates the proportion of gold out of 24 units.
It’s All about Art
Zivia is an artist at heart and has done pretty much everything art-related. She’s given painting classes to women; she’s painted murals for schools. She has illustrated some children’s books. She has even created Succah decorations for stores to sell. She never dreamed that she would one day be a jewelry designer. If anything, she was more likely to become a fashion designer. In fact, she didn’t even know that there was such a thing as jewelry design.
It began when her sister was a kallah. Her grandmother gave the new kallah money to make earrings. Zivia ended up designing the earrings. Zivia’s parents-in-law, whose family has been in the diamond trade for decades (Zivia is the fourth generation), supplied her with the diamonds and helped her find a jeweler to make the earrings. Everyone loved her sister’s earrings, and Zivia’s new business quickly took off.
“My background in art really helped with designing custom jewelry,” Zivia explains, “because a lot of jewelry design is about proportion and composition, both things that are important in art.”
(Originally featured in Mishpacha Jr., Issue 949)
Oops! We could not locate your form.